布袋除尘器-除尘设备
布袋除尘器的工作机理是含尘烟气通过过滤材料,尘粒被过滤下来,过滤材料捕集粗粒粉尘主要靠惯性碰撞作用,捕集细粒粉尘主要靠扩散和筛分作用。滤料的粉尘层也有一定的过滤作用。
布袋除尘器除尘效果的优劣与多种因素有关,但主要取决于滤料。布袋除尘器的滤料就是合成纤维、天然纤维或玻璃纤维织成的布或毡。根据需要再把布或毡缝成圆筒或扁平形滤袋。根据烟气性质,选择出适合于应用条件的滤料。通常,在烟气温度低于120℃,要求滤料具有耐酸性和耐久性的情况下,常选用涤纶绒布和涤纶针刺毡;在处理高温烟气(<250℃)时,主要选用石墨化玻璃丝布;在某些特殊情况下,选用炭素纤维滤料等。
布袋除尘器运行中控制烟气通过滤料的速度(称为过滤速度)颇为重要。一般取过滤速度为0.5—2m/min,对于大于0.1µm的微粒效率可达99%以上,设备阻力损失约为980—I470Pa 。
气箱脉冲袋式除尘器技术参数
参数 | 处理风量(m3/h) | 过滤风速(m/min) | 过滤面积(m2) | 滤袋数(个) | 阻力(Pa) | 含尘浓度(g/m3) | 保温层面积(m2) | 重量(kg) | |
型号 | |||||||||
32-3 | 6900 | 1.2-2.0 | 93 | 96 | 1470-1770 | <1000 | 26.5 | 2.880 | |
32-4 | 8930 | 124 | 128 | 34 | 4.080 | ||||
32-5 | 11160 | 155 | 160 | 41 | 5.280 | ||||
32-6 | 13390 | 186 | 192 | 48.5 | 6.480 | ||||
64-4 | 17800 | 248 | 256 | 70 | 7.280 | ||||
64-5 | 22300 | 310 | 320 | 94 | 9.960 | ||||
64-6 | 26700 | 372 | 384 | 118 | 11.640 | ||||
64-7 | 31200 | 434 | 448 | 142 | 13.320 | ||||
64-8 | 35700 | 496 | 512 | 166 | 15.000 | ||||
96-4 | 26800 | 372 | 384 | <1300 | 110 | 10452 | |||
96-5 | 33400 | 465 | 480 | 120 | 12120 | ||||
96-6 | 40100 | 557 | 576 | 130 | 14880 | ||||
96-7 | 46800 | 650 | 672 | 140 | 16920 | ||||
96-8 | 53510 | 744 | 768 | 150 | 19810 | ||||
96-9 | 60100 | 836 | 864 | 160 | 21240 | ||||
96-2×5 | 66900 | 929 | 960 | 175 | 25200 | ||||
96-2×6 | 80700 | 1121 | 1152 | 210 | 30240 | ||||
96-2×7 | 94100 | 1308 | 1344 | 245 | 35280 | ||||
96-2×8 | 107600 | 1494 | 1536 | 280 | 40320 | ||||
96-2×9 | 121000 | 1681 | 1728 | 315 | 45360 | ||||
96-2×10 | 134500 | 1868 | 1920 | 350 | 50400 | ||||
128-6 | 67300 | 935 | 768 | 125 | 24120 | ||||
128-9 | 100900 | 1402 | 1152 | 196 | 31680 | ||||
128-10 | 112100 | 1558 | 1280 | 205 | 34680 | ||||
128-2×6 | 34600 | 1869 | 1536 | 323 | 43920 | ||||
128-2×7 | 15700 | 2181 | 1792 | 247 | 52680 | ||||
128-2×8 | 179400 | 2492 | 2084 | 262 | 60000 | ||||
128-2×9 | 201900 | 2804 | 2304 | 277 | 66480 | ||||
128-2×10 | 224300 | 3115 | 2561 | 292 | 72000 | ||||
128-2×11 | 247600 | 3427 | 2856 | 307 | 78480 | ||||
128-2×12 | 269100 | 3728 | 3072 | 322 | 96400 | ||||
128-2×13 | 291600 | 4050 | 3328 | 337 | 93600 | ||||
128-2×14 | 314000 | 4361 | 3584 | 252 | 100800 |
布袋除尘器设备选购:
布袋除尘器在使用过程中如果出现清灰系统没有设计好,未按操作规程等等,这其中的任何一个细节,都可能造成布袋除尘器的除尘效果变差。这就提示用户在选购和使用除尘器时一定要考虑周全。
我们在选购除尘器时一定要把实际的工况条件如烟气的温度、腐蚀性等详细提供给布袋除尘器生产厂家,不同的工况条件使用的除尘器在结构及配件的使用上是有差别的。不能仅为追求降低成本,选择一套不适合的除尘设备。在验收布袋除尘器的时候,一定要严格按照国家相关标准进行检测,因为布袋除尘器的工作效果,还会受到一些除尘配件的制作工艺的影响,如配件的质量不好、箱体和灰斗没有缝合好,就有可能出现漏气从而影响到除尘效果。
布袋除尘器在使用过程中,突然出现除尘效果不达标的情况,这时须根据如下建议逐一排查:
1、检查是否有破袋,或者除尘布袋达到使用年限
2、喷吹系统(脉冲阀、气缸、电控柜)出现问题
3、烟气条件发生改变,如烟气中含水量增大、烟气量增大等
最后,在操作布袋除尘器的时候一定要按照供货商提供的操作规程进行,违规操作可能会损坏一些配件,导致布袋除尘器除尘效果不理想。
布袋除尘器要有良好的工作效果,是一个综合作用的结果,在生产过程中,任何一环没有注意,都会影响的布袋除尘器的质量。
布袋除尘器历史发展应用:
国内的袋式除尘器相当大的一部分采用传统的针刺毡滤料,属于深层过滤,即依靠截留在过滤材料上的微尘颗粒层进行分离,一般存在着过滤阻力大、反冲洗频率高等问题,使得除尘滤袋的寿命比较短,操作相对困难。近年来针对我国国情及冶金工业产生的高温烟气除尘用滤袋的要求,研制出了氟美斯系列耐高温针刺滤料系列,它是由二种或二种以上的耐高温纤维混合及层状复合而成,经不同的表面化学处理与后整技术,具有易清灰,拒水防油、防静电等特性,广泛用于钢铁、有色冶金、化工、炭黑、建材、电力等部门。袋式除尘器滤料的发展,主要是围绕材质、织物结构、表面处理技术这三方面来进行。20世纪50年代以前,滤料材质主要是棉、毛等天然纤维,存在使用温度低、吸湿率高、不耐酸等缺陷。20世纪70年代,随着石油工业的发展出现了合成纤维,滤料材质的发展是向使用温度高、吸湿率低、耐腐蚀等方面发展,过滤材料趋于用合成纤维和无机纤维来替代天然纤维,先后出现了玻璃纤维、芳香族聚酰胺、聚四氟乙烯(PTFE)等材质性能优良的滤料。随着袋式除尘器应用范围的扩大和环保排放指标要求越来越严格,滤料仅在材质上和织物结构上发展已不能满足要求,必须发展后处理技术,以改善滤料的物理化学性能和清灰功能,提高过滤效率。
滤料的后处理技术包括预涂层处理,热熔延压处理,表面覆膜处理等。预涂层处理,即将配制好的粉剂,用特殊工艺溶进己缝制好的滤袋滤料内部,再用黏结剂固定,达到除尘滤袋未使用前就已具有高效收尘的能力,克服了新滤料前期除尘效率不高的弊病;对针刺毡,在滤尘面进行热熔延压表面处理后,表面光滑,表面孔隙变小,有利于清灰剥离,提高收尘率,降低阻力;表面覆膜处理,即通过粘合剂黏合或热压黏合在滤料表面覆膜,通常为PTFE薄膜。表面覆膜处理形成的薄膜滤料是采用膜分离技术,实现了真正的除尘滤袋表面过滤,其过滤效率高,阻力大大降低,节约了能源,在环保要求越来越高的地区,日益得到广泛的应用。
故障分析与处理方法:
袋式除尘器运行中注意观测DCS系统显示的系统压差、入口气体温度、主电机的电压、电流等数值,以判断单机脉冲除尘器整机的运行状况正常。
原因分析 | 处理方法 |
除尘滤袋破损。 | 更换滤袋。 |
花板厚度不够,不够平整,滤袋与花板连接处有烟尘泄露。 | 更换平整光洁、厚度足够的花板。 |
清灰频率过高。 | 检查清灰系统,消除原因。 |
原因分析 | 处理方法 |
脉冲清灰系统设计不当,清灰能力不够,或者清灰不均匀,一部分滤袋清灰不足,另一部分滤袋清灰过度。 | |
清灰用的电磁阀、脉冲阀故障 | 检修电磁脉冲阀 |
清灰用压缩空气脱油、脱水不好。 | 检查油水分离器 |
压缩空气压力不够。 | 调节增加压缩空气压力。 |
锅炉的管子破裂,烟气中的水量大量增加 | 启动喷粉系统 |
锅炉负荷的提高 | 调节引风机风量 |
因缺煤而长时间而烧油 | 启动喷粉系统 |
煤种灰分太高 | 合理配煤 |
除尘器骨架锈蚀,与滤袋粘连。 | 对笼骨进行加面层处理。 |
笼骨竖筋较多,间距小,滤袋过滤面积减小,减弱了滤袋的加速。 | 减少笼骨竖筋的数量。 |
滤袋与笼骨配合不好,装配得太紧,清灰时不能正常挠曲。 | 重新安装滤袋 |
灰斗中存灰过多。 | 排走灰斗中的存灰。 |
雨水漏入除尘器。 | 检查除尘器外壳。 |
烟气通道中遗留杂物未清除。 | 清除遗留杂物。 |
原因分析 | 处理方法 |
滤料的选用不当 | 更改滤料的选用。 |
受除尘器入口气流的冲刷 | 除尘器入口设多重导流叶片。 |
滤袋与锈蚀了的笼骨钢筋摩擦 | 对笼骨进行加面层处理。 |
安装时操作不够妥善,使滤袋受损。 | 更换滤袋。 |
滤袋安装后垂直性和平行性不好,相互碰擦。 | 手动微调,使除尘滤袋间保持较为相等的距离。 |
清灰空气压力过大。 | 调节清灰压缩空气压力。 |
清灰频率过高。 | |
滤袋阻力过大。 | |
在频繁的经过酸露点的状况下使用除尘器。 | 限制在气体温度降至酸露点下使用除尘器。 |
烟气温度突然升高而旁通失灵。 | 检查旁通提升阀。 |
2、运行中注意观测DCS系统显示的系统压差、入口气体温度、主电机的电压、电流等数值,以判断单机脉冲除尘器整机的运行状况正常。
3、巡视检查各孔门、检查门及管道连接处应严密无泄漏。
4、检查卸灰装置运行工况,如有卡堵现象,应立即处理。
5、检查电动机电流指示应正常、温度、振动不得超过规定值,运转声音无异常。
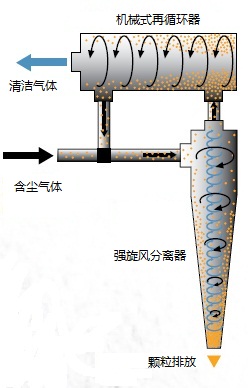
开机顺序:
单机脉冲除尘器在安装完毕后或者长期停机后再次启动时应进行仔细检查:
1.1 注意检查壳体所有连接处是否紧固,需要密封处密封得如何,焊接是否不漏气,花板是否水平,加热装置应完好可靠,除尘器的梯子、平台、栏杆清洁、牢固可靠且照明充足。
1.2 进行结构检查完后再检查滤袋,滤袋和笼骨的安装配合得是否完好,安装在花板上的笼骨和滤袋的顶部是否严密不漏气;再到灰斗内检查滤袋是否碰撞,可用手微调。
1.3 然后检查机械部件,看进气、排气、旁通阀门能否完全开启,严密关闭,能否锁住,并验证限位开关,各传动机构完好,润滑良好。
1.4 对清灰系统应气包、脉冲阀、喷吹管三者之间的连接有无漏气,喷吹孔是否对准除尘布袋中心,是否有堵塞现象,还要听脉冲声音是否正常。
1.5 对压缩空气系统要检查过滤器、干燥器工况是否良好,空气压缩机是否到一定压力后即自动关机。如未关机,应检查压力开关和控制装置是否正常。空气压缩机应有安全阀,要检查其能否正常工作。
1.6 对控制系统要验证PLC的运行情况。此外还需要检查除尘系统的风机的工况是否良好。所有仪表、电源开关、调节器、监视及报警信号、保护装置的功能完好。
2、初次启动操作方法
经检查除尘系统安装良好可供使用后,初次启动的操作方法为:
2.1在启动前至少8h即向灰斗加热器通电加热。
2.2在锅炉离线的情况下,利用引风机将一层粉料敷在除尘滤袋上。预敷粉料为冷态下通过灰罐车在烟道内喷入约60吨飞灰或生石灰粉。敷粉的操作方法如下:
2.2.1在敷粉前开动除尘器的输灰系统。
2.2.2关上旁通提升阀,打开分室的排气提升阀和进气碟阀。
2.2.3在敷粉过程中应断开所有分室的清灰定时器,以防滤袋意外清灰。
2.2.4关上引风机入口的控制阀门,然后开动引风机。当引风机达到满速度,即慢慢地打开入口阀门,不要超过引风机的电流额定值。敷粉时需要有适当的气流量,以免粉料落入灰斗。如发现粉料沉降太多,则需要增加风量。可以每次两个分室依次进行,直至敷完。
2.2.5在空气预热器出口烟道上设置喷粉管,并留有接口,利用灰罐车气力输送喷粉,将粉料从除尘器上游管道上孔口加进去,管道内保持15m∕s的风速,以免粉料沉降。最好使每个分室的花板压差增加值达到125Pa,即上升至超过初始读数125Pa。这时应测定气流量,以验证125Pa增长是由于滤料敷粉,而不是风量的增加。
2.2.6在敷粉的过程中,最好能查看一下花板的漏尘情况,找出破损的除尘滤袋,予以更换。因为一旦完成敷粉,将分室与引风机隔离,有一些粉料会降落在花板上,就不容易看出花板上的漏尘情况。
2.3完成敷粉后,锅炉应在24h内开始燃烧天然气等辅助燃料。在锅炉用辅助燃料升温的同时,也让袋式除尘器预热。待除尘器预热出口温度稳定于1250C时,锅炉即可开始烧煤。
2.4在预热之初,应将除尘器置于旁通,以预热进气和排气总管。然后打开除尘器分室阀门,关上旁通提升阀门。这样,热量集中于较少的分室,可以加快预热过程。
2.5在启动时,花板压差达到1000~1300Pa以前,不应为滤袋清灰(通常大约需要4~6h,最长可能要12h)。在第一个清灰周期以后,即可用自动模式清灰。在开头的清灰周期内,滤袋上的粉量可能很多。因此,需要增加两个分室之间的清灰静止期(达15min),以免输灰系统过负荷。
2.6如果启动期间锅炉被迫停炉,而停炉前锅炉运行不足48h,则下次启动时必须再预敷粉料。
3、一般启动方法
在锅炉正常停炉后,袋式除尘器离线1天或更多天数后恢复在线时,应采用下列启动方法:
3.1 在启动前至少8h即向灰斗加热器通电加热。
3.2 关闭自动清灰模式。这时应当让尽可能的灰留在滤袋上。
3.3 驱动所有出口提升阀和入口蝶阀,留在打开的位置。
3.4 关闭旁通提升阀。
3.5 关闭头4个分室的出口提升阀。(初步设定为2~4分室,便于集中热量进行预热)。
3.6 使锅炉在线(使用正常的锅炉启动程序)。
3.7 当除尘器排气温度达到1200C时,开始打开其后的分室,直至所有分室都打开。
3.8 将除尘器的清灰设在自动清灰模式。
4、袋式除尘器的停机
当锅炉正常停炉的情况下,袋式除尘器的停机操作方法如下:
4.1关闭自动清灰模式,在设备冷却下来以前,对所有分室的滤袋循环清灰两次。但如果提前知道停炉时间,应预先采取停止清灰措施。如停机不超过24h,就不要清灰,让除尘滤袋上粉尘在再启动时起敷粉料的作用。
4.2 当除尘器入口温度降至1250C时,即开始用辅助燃料燃烧器来稳定气体温度,直至煤火熄灭。
4.3 继续运转引风机1h,清除除尘器所有分室内残留的酸性气体,然后停止引风机运转
4.4 输灰系统继续运行,在整个停机过程中应保持灰斗加热,直至把灰斗中的灰全部排空。
4.5 打开除尘器的旁通阀门。
4.6 关闭除尘器上的出口阀门。
4.7 关闭入口蝶阀。但应注意,如果排灰系统还在运行时则不应关闭入口蝶阀。因为这会在滤袋上造成过大的压力,将滤袋上的粉尘拉脱,从而使滤袋受潮。
4.8 袋式除尘器应保持旁通状态,直至准备恢复在线,然后即按“一般启动方法”执行。
技术资料
- 绥化市吊钩式喷砂机_绥化市吊钩式抛丸机_绥化市吊钩式抛丸除锈清理机_绥化市吊钩式喷丸设备提高板材的预加工质量?
- 鄂尔多斯6915钢管除锈抛丸机调试完毕
- 2018发往山东临沂吊钩式378抛丸机
- 通过式抛丸清理机发往胶州的装货现场
- 环保型吊钩式抛丸机发货现场
- 淄博钢结构抛丸机使用现场
- 黄骅悬链式抛丸机客户现场
- 路面抛丸机应用于广州桥面建设
- 履带式抛丸机客户案例现场汇总
- 布袋除尘器-除尘设备
最新资讯文章
- 履带式抛丸机如何提高工作效率
- 路面抛丸机的材料适应性与表面粗糙度测试研究
- 型钢抛丸机对产品质量的影响解析
- 高效能路面抛丸机的性能考察
- 不同类型抛丸机的选购指南
- 路面抛丸机的作业技巧解读
- 路面抛丸机的节能减排技术探索
- 吊钩式抛丸机的维护保养指南
- 喷砂房环境保护措施与建议
- 通过式抛丸机的操作实例分享